Pirelli è l'unica azienda al mondo che produce pneumatici per bici in Italia a livello industriale. Nello stabilimento di Bollate, in provincia di Milano, nascono i modelli top di gamma dei segmenti road, gravel e mountain bike, che attualmente rappresentano la centralità dell'intera fornitura Pirelli. Sono realizzati da una linea altamente automatizzata che assicura il massimo della qualità, non solo del prodotto ma anche del luogo di lavoro e dell'ambiente.
Da questo punto di vista Pirelli è all'avanguardia: l'esperienza sulle linee produttive di alta tecnologia inizia verso la fine degli anni Ottanta, con l'inaugurazione di una delle prime fabbriche al mondo di produzione pneumatici completamente automatica (per auto). Con la stessa logica avanzata, messa a punto con il tempo e con l'esperienza, è nata l'attuale unità cycling a Bollate, dove è installata la più recente linea produttiva per pneumatici da bici, realizzata ad hoc dal dipartimento Pirelli che progetta e produce macchinari. È stata inaugurata nel 2022 al termine di un complesso processo di riconversione industriale iniziato nel 2019.
Perché l'alta automazione assicura la qualità di un pneumatico? Per scoprirlo vediamo passo passo la nascita di un prodotto.
Nasce delicato, finisce robusto
Sappiamo tutti che un pneumatico è decisamente robusto, tanto che a seconda del tipo può equipaggiare qualsiasi mezzo, dal camion alla bici. Tuttavia nella fase di lavorazione che precede la vulcanizzazione i semilavorati che lo compongono sono molto delicati, tanto che maneggiandoli si corre il rischio di danneggiarli. Per estremizzare il concetto si può dire che il miglior processo produttivo è quello asettico: meglio evitare il contatto manuale e rendere ogni operazione il più possibile automatizzata, fin dall'arrivo dei componenti, tele, mescole, parti rinforzate e altro, ed è proprio con questo obiettivo che è stato realizzato lo stabilimento di Bollate.
Inoltre un processo automatizzato altamente evoluto assicura la massima precisione del prodotto finito, qualità di fondamentale importanza per ogni pneumatico e in particolare per i leggerissimi e sottili modelli per bici.
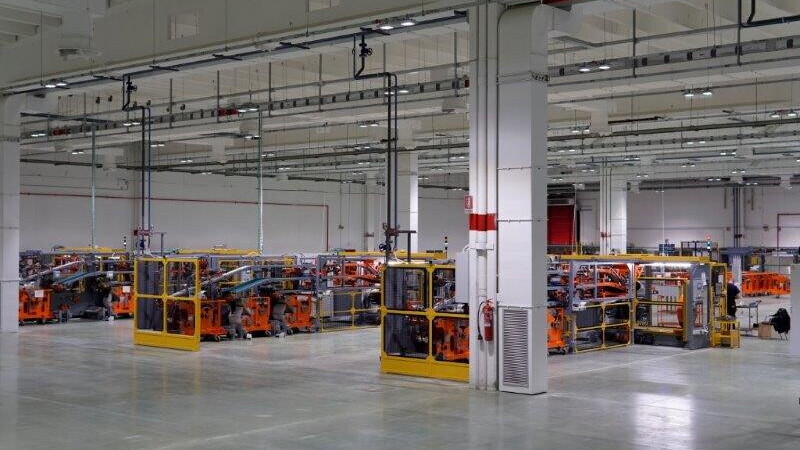
Il ciclo produttivo
La linea dello stabilimento di Bollate è costituita da un corridoio centrale dove avviene il confezionamento. Qui nasce il pneumatico finito, completo di tutti i componenti; poi passerà alla vulcanizzazione. Ai lati del corridoio ci sono le aree di produzione dei semilavorati, con le macchine divise in due gruppi: da una parte si preparano le tele; dall'altra si profilano i battistrada.
Al momento ci sono diversi punti di confezionamento, destinati alle tre linee di prodotto (road, gravel e mountain bike).
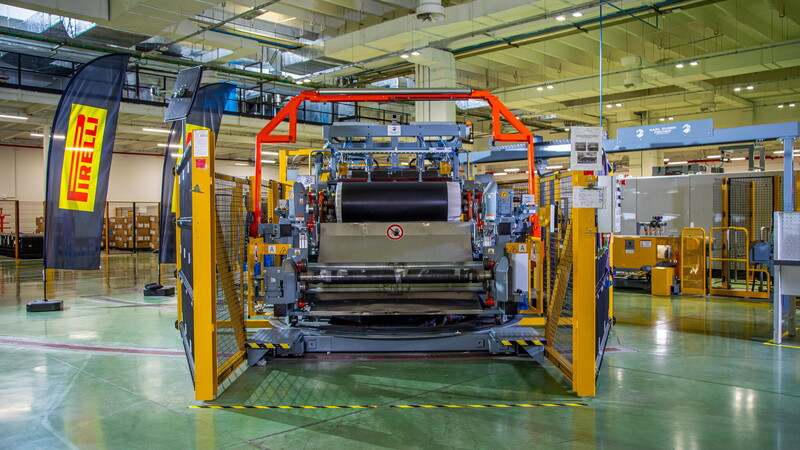
La costruzione della carcassa
Gli elementi fondamentali di una carcassa sono la fascia di tessuto e la qualità delle mescole, e il know-how Pirelli abbraccia entrambi i settori, grazie all'esperienza accumulata nella produzione di pneumatici ad alte prestazioni.
Per la realizzazione della carcassa si usa un tessuto gommato di spessore sottile (alcuni decimi di mm), con trama in poliammide ed eventualmente inserti in fibra aramidica, materiale tecnologicamente avanzato. Queste tele arrivano in azienda avvolte in bobine e passano nelle macchine di taglio, che le preparano nella larghezza adeguata alla tipologia di pneumatico, quindi con strisce che vanno dalle più strette per le gomme road alle più ampie per le mountain bike.
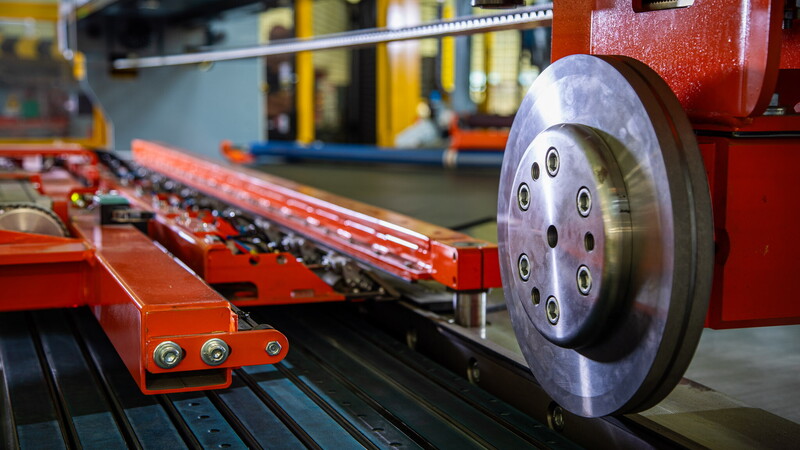
Fascia battistrada
Il cuore della fascia battistrada è la mescola, punto di forza di formulazione Pirelli, che arriva in forma di tubi dallo stabilimento di Slatina in Romania o da Settimo Torinese. Con questa si genera la fascia battistrada, che per una gomma road è a forma di mezzaluna molto sottile. È di basilare importanza poiché appoggia al suolo e definisce le prestazioni del pneumatico: la scorrevolezza, l'aderenza, il consumo.
Si ottiene a partire dai bordioni con un processo di estrusione eseguito da una trafila di progettazione Pirelli: una tramoggia lavora la mescola realizzando il tipo di fascia battistrada richiesto. A valle del processo ci sono i controlli strumentali che verificano i parametri del profilato (temperatura, larghezza, spessore) e infine passa nel tunnel di raffreddamento. La macchina permette di realizzare anche una fascia battistrada bimescola.
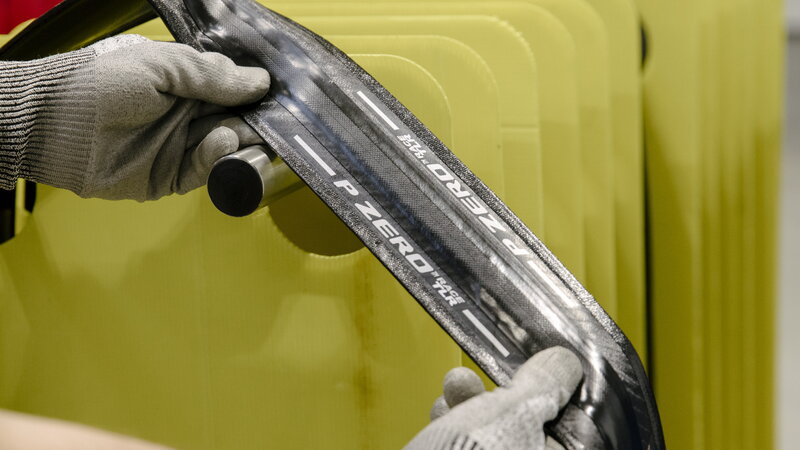
Il confezionamento
La confezionatrice è costituita da un tamburo sul quale si avvolgono tutti i componenti del pneumatico. La procedura inizia con la costruzione della struttura di carcassa che comprende almeno l'alimentazione della/e tela/e pretagliata/e, cui si aggiunge al termine della confezione stessa la fascia battistrada. Secondo il modello di pneumatico da confezionare sono poi previsti ulteriori componenti quali ad esempio rinforzi di varia tipologia, strati antiforatura, e strati di impermeabilità per i pneumatici di tipo tubeless (TLR).
L'intero processo è eseguito in modo automatizzato e sicuro, con l'operatore lontano dai macchinari in lavorazione.
A questo punto il pneumatico è finito in tutte le sue parti ma è ancora in forma delicata, poiché manca il processo di vulcanizzazione. Per comprendere il concetto si può pensare a una sorta di consolidamento dei componenti, che ha il risultato di fissare il tutto trasformando le mescole nella loro forma più resistente.
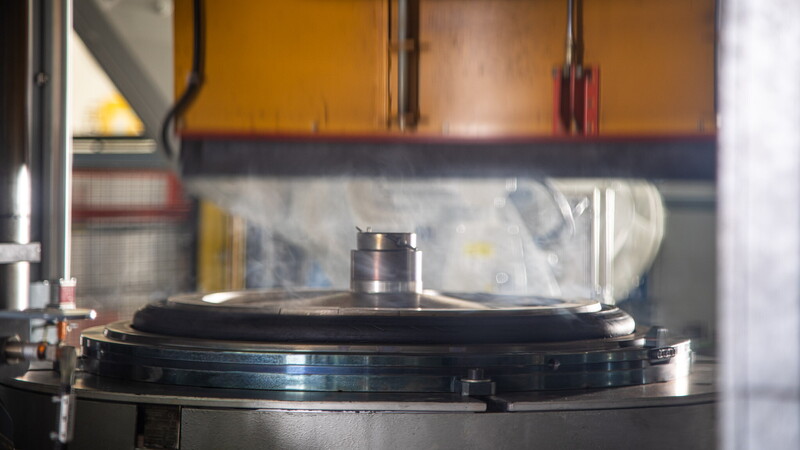
Vulcanizzazione: il processo finale
La vulcanizzazione trasforma le mescole dallo stato plastico a quello elastico rendendo il pneumatico uniforme, maneggiabile e pronto per essere installato sulla bicicletta. Si ottiene predisponendo un pneumatico “crudo” su un dispositivo di manipolazione in prossimità dello stampo: da quel momento in poi l'operazione è eseguita in modo completamente automatizzato. Il ciclo può essere di pochi minuti, con variazioni a seconda del tipo di pneumatico di temperatura, pressione e/o tempo. Al termine il prodotto finito è inviato, sempre automaticamente, al controllo qualità.
I macchinari di vulcanizzazione necessitano di attenzione dal punto di vista ambientale perché producono calore e fumi, e per questo sono racchiusi in una cabina coibentata dotata di aspiratori, sistema che offre tre vantaggi: permette di mantenere stabili le condizioni dell'operazione, importanti per garantire la qualità del prodotto; assicura un ambiente confortevole agli operatori poiché all'esterno della cabina il clima è controllato; favorisce il risparmio energetico limitando la dispersione di calore.
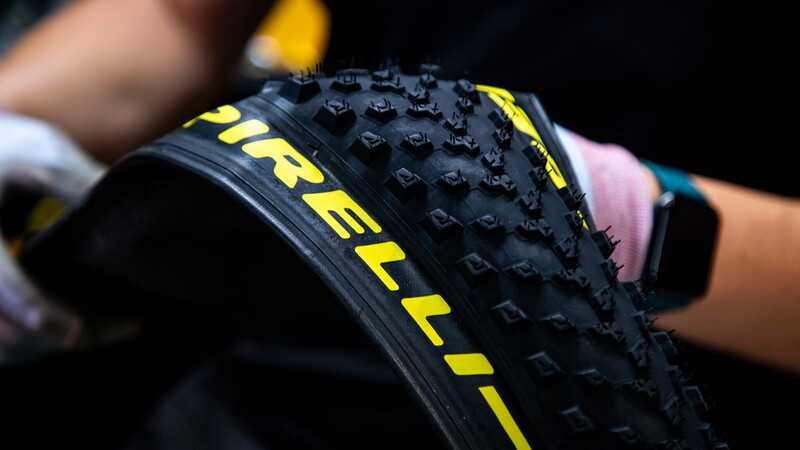
Il controllo di qualità
Ogni pneumatico passa infine al reparto di controllo qualità, dove viene esaminato da ogni punto di vista. Il processo è eseguito manualmente da operatori specializzati che verificano lo stato del prodotto finito nel minimo dettaglio e scartano in presenza di non conformità di prodotto.