Pirelli has a five-year partnership with Princeton University. In an example of some of the University's pioneering research, Assistant Professor José Avalos explains why the fuel that powers our vehicles may soon be coming out of a vat rather than a hole in the ground.
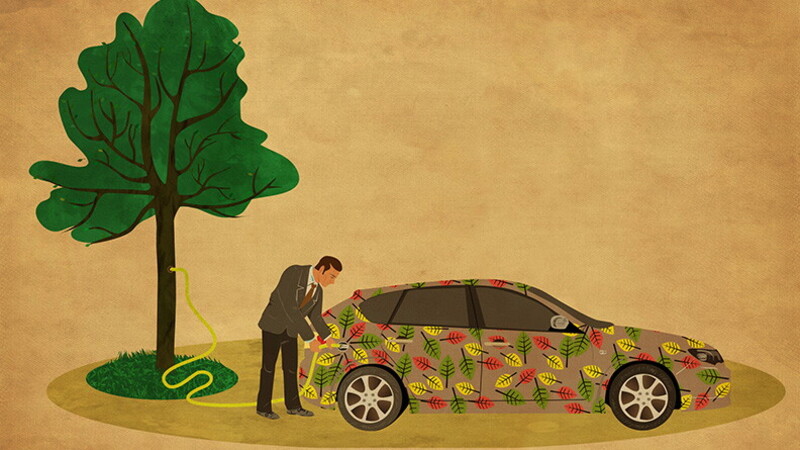
When it comes to fuelling your car, petrol is hard to beat. It is cheap, available everywhere and its energy density means it gives you a better result for your money than any alternative.
But some people are trying to better it – and do away with its downsides of CO2 emissions, supply issues and the environmental damage caused by extracting and using it, especially its contribution to climate change. Among them is Assistant Professor José Avalos, who is jointly appointed to Princeton University's chemical and biological engineering department and the Andlinger Center for Energy and the Environment.
Avalos is passionate about biofuels, which, as their name implies, are fuels derived from biological rather than geological sources. All are renewable and some, like biodiesel, come from the oils produced by crops such as rapeseed.
But other biofuels, the ones that interest Avalos, are brewed. The most widely-used biofuel today is ethanol – the alcohol that many yeasts make during fermentation.
“It's what yeasts make naturally,” he says. “Most of their metabolism is put towards ethanol production.”
Concentrated effort
As well as being easy to make in large quantities, ethanol can be mixed with petrol so it can be burned in existing engines. Despite this it does have drawbacks that prevent it making up any more than 15 per cent of the diet of gasoline-burning internal combustion engines.
To begin with, ethanol is corrosive and naturally absorbs water from the surrounding air. Both these aspects are obviously problematic for transporting and storing a fuel and then setting light to it; you are probably going to have an explosion at some point.
Good candidates for replacing ethanol are heavy alcohols that go by the formidable names of isobutanol and isopentanol. These fit the bill because they have an energy density closer to that of petrol. However, their true advantage lies in their much higher compatibility with infrastructure than ethanol, so they can potentially be used at much higher blends with gasoline. This means that heavy alcohols would make it possible to replace a larger percentage of petroleum gasoline with renewable biofuels with no changes to existing infrastructure or engines.
But, says Avalos, they are tricky to make in large quantities because yeast would much rather make ethanol.
“We need to trick the cell into making something other than ethanol,” he says, adding that his method of accomplishing this involves two allied techniques – metabolic engineering and directed evolution.
Metabolic engineering involves tinkering with a cell's chemical processes and the genes that direct them, to make it produce far more of a substance than it would normally. Yeast is a great organism to work with, says Avalos, not only because it has been so closely studied over many decades, and because there are so many fantastic genetic tools to engineer it, but also because it is an industrial workhorse, much more tolerant to the toxicity of alcohols than other industrial hosts, and is already the foundation for most of the bioethanol industry today.
Culture vultures
Armed with the knowledge about the metabolites at each stage and the enzymes that control the reactions to produce new molecules, as well as the tools to modify them, Avalos and his research team have been able to tinker with the cellular cascades of enzymatic reactions in what's called “metabolic engineering”.
“We try to genetically modify the strains so they overproduce the enzymes that are in the metabolic pathways we are interested in, and stop producing the enzymes that make ethanol” he says.
By continually breeding new strains of yeast via metabolic engineering, it becomes possible to slowly create a version that makes less ethanol and more of the other, desirable heavy alcohols. This involves adding, deleting and modifying genes so the yeast is tricked at many different stages into doing what the Princeton researchers want rather than what it naturally does. Intervening at many different steps in the lengthy chemical process known as a metabolic pathway, means small increases in the production of isobutanol or isopentanol are multiplied as the reactions roll on. At some point, with their ethanol production capacity removed, and those of heavy alcohol production added, the yeast might learn to like making heavy alcohols through directed evolution involving random mutations and adaptations – eventually, perhaps, they may even evolve to have their heavy alcohol production be essential for their survival.
So far, Avalos is remaining tight-lipped about just how much progress he and his team have made in producing yeast that churns out heavy alcohols rather than ethanol. The work is “going very well,” he says, adding that the team will begin to publish its results in peer-reviewed journals soon.
The next step will be to develop strains and manufacturing methods to produce heavy alcohols from the inedible parts of plants to increase their sustainability, and have all this work at large scale. “It needs to be cheap enough literally to burn,” he adds.
Soon after that, isobutanol and isopentanol could be found in pumps on garage forecourts. He believes the switch could take place quite quickly because the greater use of ethanol, even with its drawbacks, has put infrastructure in place in the petrol supply chain that will make changing to a better biofuel much easier.
“Ethanol is an imperfect biofuel, but it's helpful for us because when better biofuels are launched they will have an established industry to land on that is ready to take them on,” he says.
Pirelli launched a five-year partnership with Princeton University in 2014 in the field of humanities and mass media. It is one of 14 university collaborations forged by Pirelli to promote scientific and cultural research.