Pirelli is the only company in the world that produces bicycle tyres in Italy at an industrial scale. At the Bollate plant, just outside Milan, the top-of-range models are born for the road, gravel, and mountain bike segments, which at present represent the heart of Pirelli's entire supply. They are produced on a highly automated production line which ensures maximum quality, not only for the product but also for the workplace and environment.
From this point of view, Pirelli is at the cutting edge: the experience with high technology production lines begins towards the end of the 1980s, with the inauguration of one of the first completely automated tyre production factories in the world (for cars). With the same logic, put together with time and experience, the current cycling unit at Bollate was created, where the most recent production line for bicycle tyres is installed, created ad hoc by the Pirelli department that designs and produces machinery. It was inaugurated in 2022 at the conclusion of a complex industrial conversion process begun in 2019.
Why does ahigh level of automation ensure the quality of the tyre? To learn this, let's look at the birth of the product step by step.
Delicate at birth, robust in the end
We all know that tyres are decidedly robust, so much so that according to the type you can equip any vehicle, from trucks to bicycles. Nevertheless, in the process that precedes vulcanization the semi-finished components that constitute it are very delicate, so much so that by merely handling them you risk damaging them. To emphasize this concept, you could say that the best production process is the most aseptic one: better to avoid manual contact and make the operation as automated as possible, right from the arrival of the components, textiles, compounds, reinforced parts and so on, and it is precisely for this purpose that the Bollate plant was devised.
In addition, the highly evolved automated process ensures the maximum precision in the finished product, a quality of fundamental importance for every tyre and particularly for the very light and htin modles for bicycles.
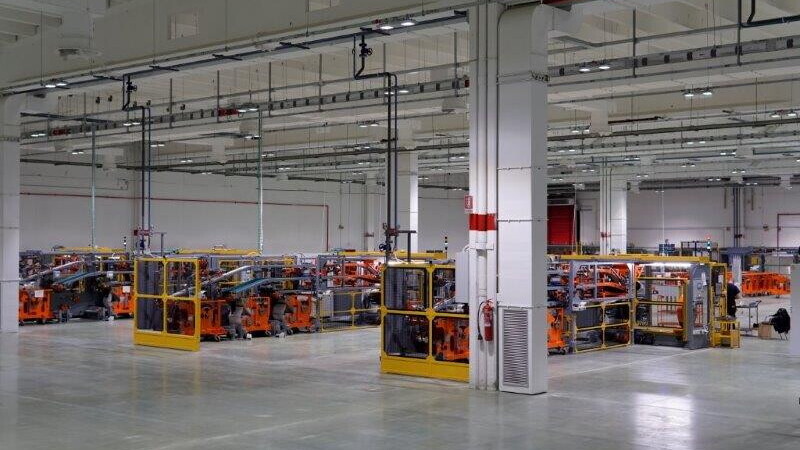
The production cycle
The line at the Bollate plant consists of a central corridor where the product is put together. This is where the finished tyre is born, complete with all its components; it then passes to vulcanization. To the sides of the corridor are the areas for the semi-finished products, with the machines divided into two groups: on one side the textile components are prepared; on the other the treads.
At the moments there are different assembly points, destined for three product lines (road, gravel and mountain bike).
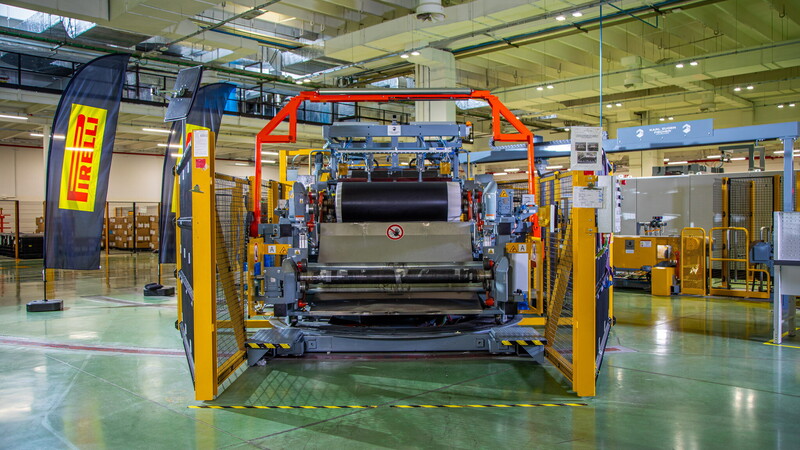
The construction of the casing
The fundamental elements of the casing are the fabric bands and the quality of the compounds, and Pirelli's know in both areas thanks to the experience gained in the production of high-performance tyres.
To create the casing, you use a very thin rubberized fabric (a few tenths of a millimeter), with polyamide pattern and eventually aramid fibre trims, a technologically advanced material. These fibres reach the factory wrapped into bolts and are passed through the cutting machines, which prepare them in the right width for the type of tyre, therefore with ribbons that go from the thinnest for road tyres to wides for mountain bikes.
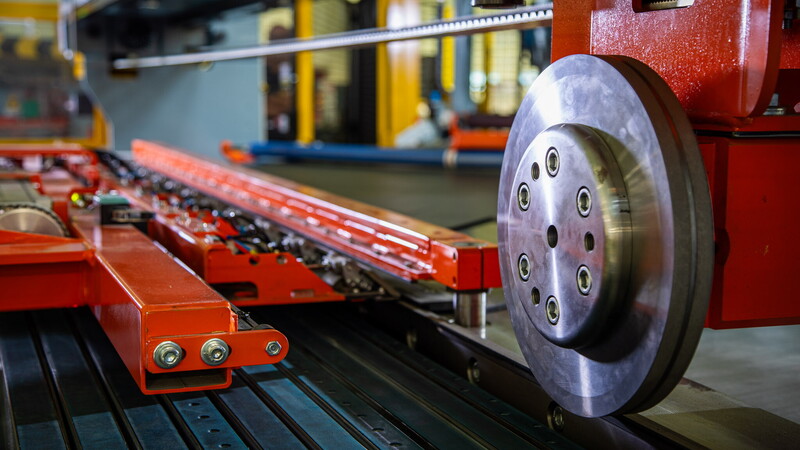
Tread
The heart of the tread band is the compound, the strong point of Pirelli's formulation, which arrives in tube form for the plant in Slatina in Romania or from Settimo Torinese. With this the tread band is produced, which for a road tyre takes the form of a very thin half-moon. It is of basic importance because it sits on the ground and defines the tyre's performance: the smoothness, the grip, the wear.
It begins with the borders with an extrusion process performed by a die designed by Pirelli: a hopper works the compound producing the type of tread band required. Downstream of the process are the checking instruments that verify the parameters (temperature, width, thickness) and finally it passes through the cooling tunnel. The machine also enables the production of bi-compound tread bands.
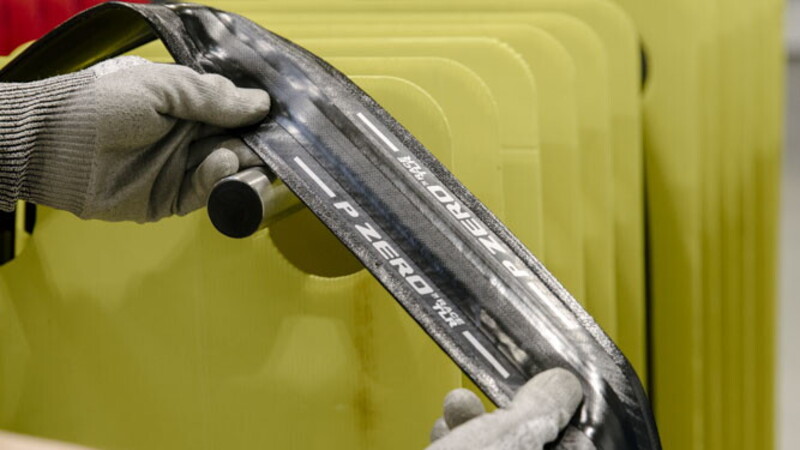
The assembly
The assembling machine consists of a drum around which all the tyre's components are warapped. The process begins with the construction of the structure of the casing to which the tread band is added at the end of the assemblage. Depending on the model of the tyre being put together other components are foreseen such as reinforcements of different types, anti-puncture layers, waterproofing layers for tubeless tyres (TLR).
The entire process is automated and safe, with the operator far from the production machinery.
At this point the tyre is finished in all its parts but is still in a delicate form as it is yet to be vulcanized. To grasp the concept, think of a kind of consolidation of the components, which results in the fixing the whole and transforming the compound into its most resistant form.
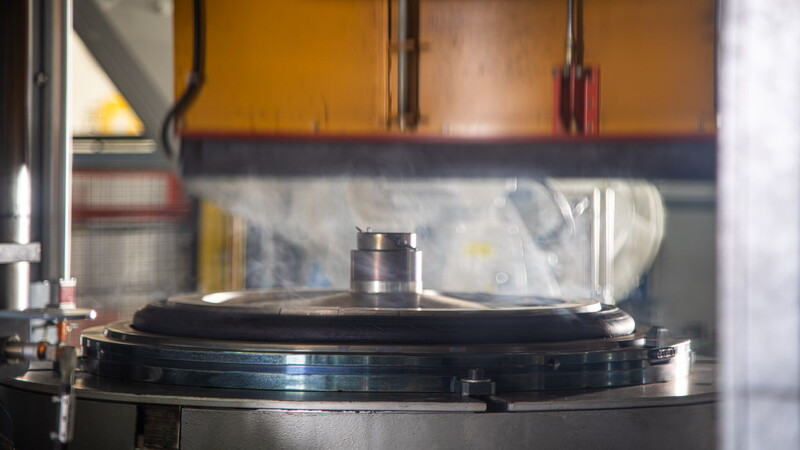
Vulcanization: the final process
Vulcanization transforms the compounds from the plastic state to the elastic, making the tyre uniform, manageable and ready to be fitted onto a bike. It is achieved by predisposing a “raw” tyre on a handling device near the press: from that moment on the operation proceeds in a totally automated manner. The cycle can take only a few minutes depending on the type of tyre, temperature, pressure and/or time. Afterwards the finished product is sent, always automatically, to quality control.
The vulcanizing machinery must be monitored from the environmental point of view because it produces heat and fumes, and for this reason they are enclosed in a cabin fitted with aspirators, a system which offers three advantages: it allows you to keep the conditions of the operation stable, important in guaranteeing the quality of the product; it ensures a comfortable environment for workers because outside the cabin the temperature in controlled; it favours energy conservation by limiting heat dispersion.
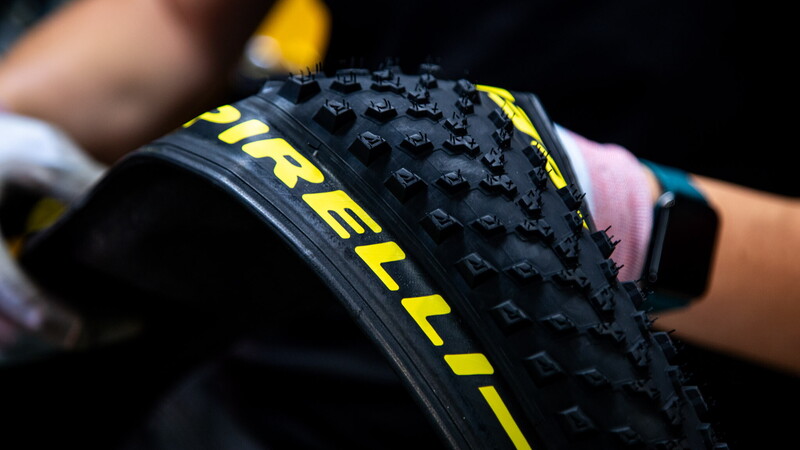
Quality control
Each tyre then goes to the quality control department, where it is examined from every point of view. The process carried out manually by workers who verify the state of the finished product in every detail and eliminate those with any imperfection.