Zen and the art of microeconomics
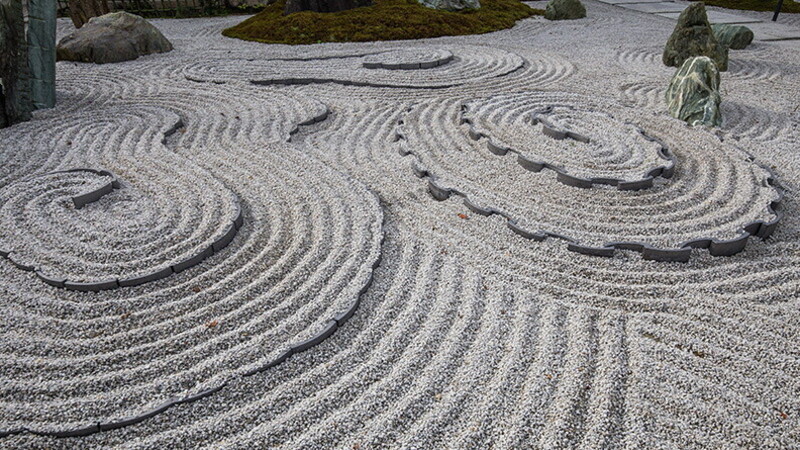
Two words (which in English become one): kai-zen, or “continuous improvement”. This is Zen translated into microeconomics, the Japanese road to corporate enlightenment: no waste, no errors, nothing left to chance. Perfectionism as a daily revolution. The philosophy developed in 1986 by Masaaki Imai changed Western business management through concepts like lean manufacturing, total quality management (TQM), Statistical process control and Just In Time (JIT). The father of Kaizen is now 87 years old and continues to take his philosophy around the world. After a long period as Toyota's number one consultant and one of the creators (along with Taiichi Ohno) of Toyotism, he founded the Kaizen Institute, which is now present in 22 countries. And he has no intention of slowing down. “There is still a lot of work to do,” he says. “If Western companies had fully adopted the kaizen philosophy, there would not now be so much talk of crisis.”
Does that mean that companies have not put your theory into practice the right way?
Theory is one thing, practice is another. It has to be a daily discipline, leaving nothing to chance.
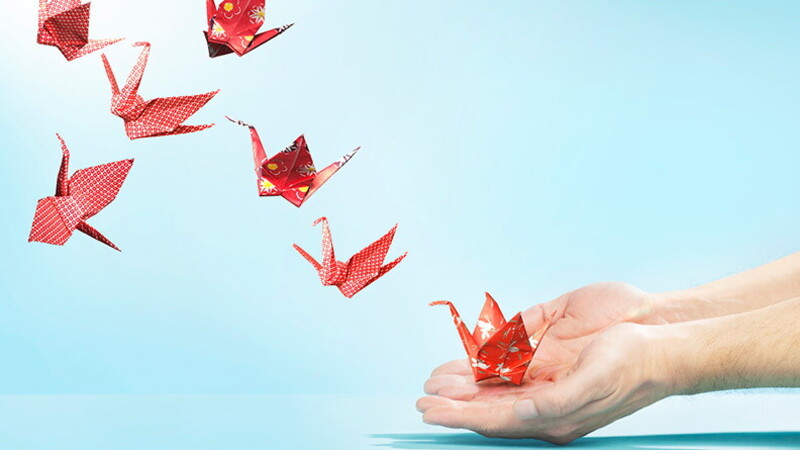
The 2008 crisis and also the current crisis have perhaps been the worst that the kaizen concept has ever faced, worldwide. Did kaizen really help businesses in dealing with the crisis?
It was industry that the crisis hit and not kaizen. Some firms survived the crisis through the application of kaizen, but the majority of them failed to embrace kaizen as the means of getting through the crisis because their top management failed to introduce kaizen as a means of overcoming the crisis.
Do you mean that companies are failing to go beyond simply cutting costs?
Cost-cutting is only a temporary means to achieve lower costs. To recover from the crisis requires an overall managerial approach to improve the three major customer requirements of QCD (quality, cost and delivery). The spirit of lean concept, as conceived by Kiichiro Toyoda, the founder of Toyota Motor Company, starts when the customer orders arrive and finishes with customer satisfaction: every internal activity in between must be taken care of, in order to really overcome the crisis.
How would you explain the concept of kaizen today to company employees who are not familiar with it?
Nowadays, I explain the meaning of kaizen not as a continual improvement but as improvement every day, by everybody and everywhere.
A constant commitment that presupposes great order and nothing being left to chance. Is that correct?
It actually requires tremendous self-discipline and determination. And in order to be effective, it should be carried out by all members of a firm, not only involving workers but also involving all management: as I said, every day, everybody.
And everywhere?
Yes. This means that improvement must be carried out not only on the shop floor but also in all the other corporate functions.
In practical terms, what are the essential tenets of kaizen that cannot be ignored?
It depends on which level it is applied. In day-to-day operations on the shop floors, improvement can be achieved by employing everybody's common sense, using unsophisticated problem-solving tools.
Can you give us an example?
For instance, a first step might be to let the employees become aware of waste in the office and service area: waste of time, space, human and material resources. Then, workplaces can host wider value creation initiatives, achieved through everybody's cooperation.
In other words, just tidying up the office is not enough.
Of course it is way more complicated than that. A lean office transformation, in a bank, insurance company or even in a local government body, begins by visualising their processes and their targets, organising teams around daily and project-based kaizen activity, and building simple performance management systems.
And what would you say to the managers of today?
Managing a firm through kaizen requires the use of statistical tools, however, there are also various non-statistical tools that have typically been developed by lean companies, notably by Toyota for minimising variability in production, such as standardisation, introduction of Takt time, synchronisation, shortening the total production lead time.
So a lean company means order at its purest?
It simply means efficiency and total optimisation. Application of Just-in-Time, Kanban, pull systems, and other lean production and lean logistics methods will create a more flexible supply chain, with lower inventory levels and increased productivity.
Never leave anything to chance: but does standardisation not bring the risk of losing out in terms of creativity?
The standard is not set in stone. The definition of a standard is that it is the best way to do the job for now. It should be regarded as a stepping stone towards further improvement.
What is the difference between kaizen and a normal corporate reorganisation?
The maintenance and improvement of workplace standards is a daily activity that must be done by the natural teams who are closest to the work. Project-driven improvement is not true continuous improvement involving everyone, every day, everywhere. The Daily Kaizen system engages the creativity of people at all levels to improve their own work. Not only does this help to sustain operational effectiveness, it improves teamwork.
A very oriental concept. How has it been received by Western companies?
To adopt a theory is always easier than to put it into practice. I believe that the kaizen concept has been well understood throughout Western businesses but, there are still large margins for putting it into practice in daily operations.
MASAKI IMAI
Masaaki Imai (1930) is a Japanase management theorist, best known for kaizen.