The need for carbon
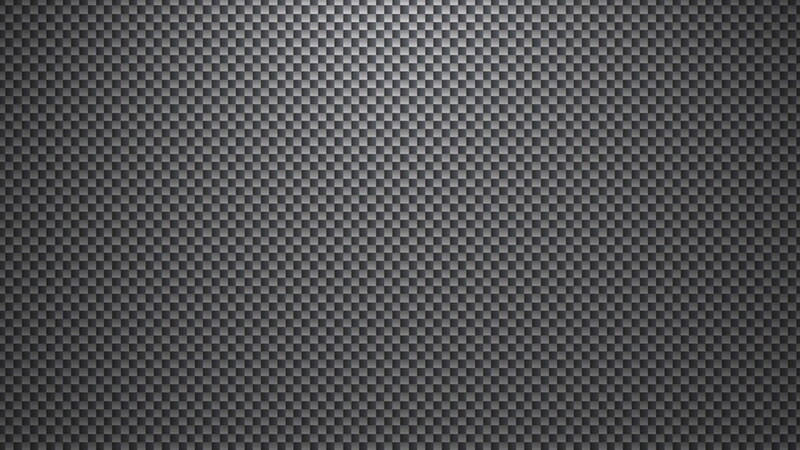
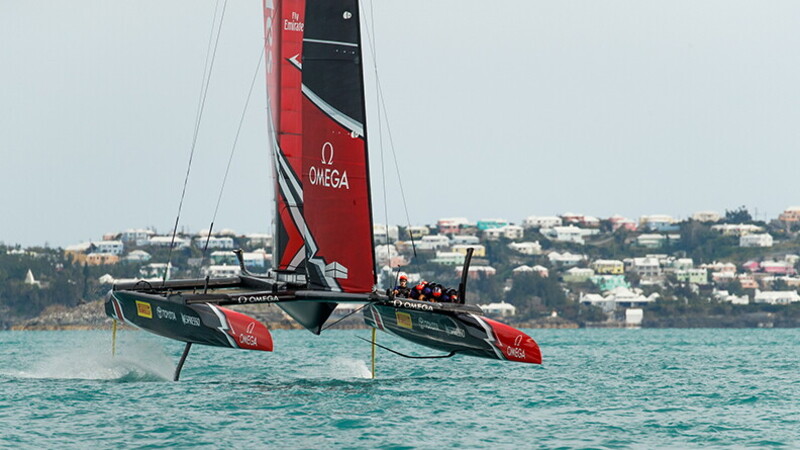
Black carbon-fibre is the boat building material for the America's Cup. Once only used for high-tech objects, it is now widely available and much cheaper to produce, and so found in innumerable everyday items. On a more general note, man's use of composite materials goes back thousands of years. You may smile, but primitive huts made from mud and straw represent one of the very first examples of uniting a fibre with a matrix or resin. The fibre offers the best mechanical characteristics, while the matrix holds the product together. Today, fibreglass – a combination of glass fibre and various resins – is the most well-known composite: it is found in many guises in our homes. A composite material made from carbon fibres and epoxy resins has amazing mechanical properties. It can consist of multiple cross-laid layers of a single “skin” or take the form of a “sandwich”, where a neutral layer (usually a lightweight material to add thickness) sits between two surface skins. Carbon-based composites are now used to build aircraft, cars, boats, bicycles and even musical instruments. First used in the 1980s, perhaps the best known application is the famous Stealth aircraft, that ‘invisible' plane used in the Gulf War. Today, carbon is used widely in racing, for cars and boats alike: nearly every Formula One car has a driver's seat made from carbon-fibre for lightness and, above all, safety; likewise, the AC 50 Class boats in the America's Cup contain a lot of carbon-fibre. These foiling catamarans are currently racing in Bermuda to the delight of all.
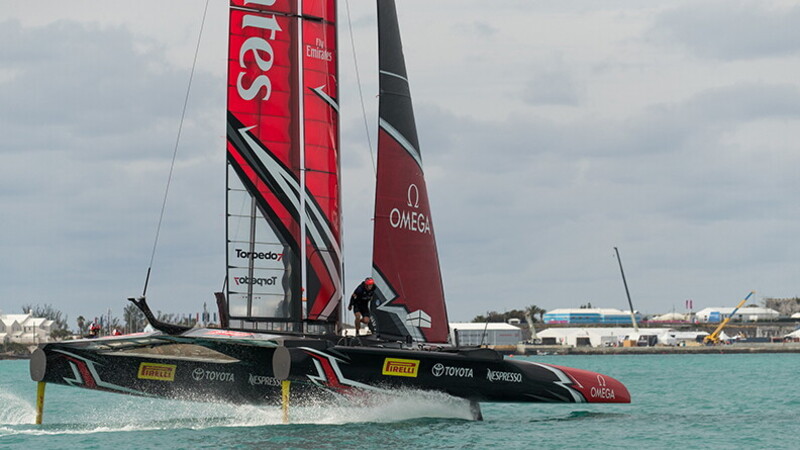
The first car to have its entire chassis made from carbon-fibre was the McLaren in 1982. Since then, the technology has evolved considerably and carbon-fibre is now used to build most parts of a racing car. Indeed, if it weren't for the strict regulations that limit its use, carbon-fibre might also be used to build most engine parts. This multipurpose material has now replaced titanium, only used when strictly necessary. Carbon-fibre is the perfect solution if you want maximum rigidity and excellent strength but minimal weight. It's a ductile material, meaning you can easy mould it into any shape. It's changed the shape of our cars to great advantage in various disciplines, from a car's aerodynamics to its aesthetics. In the early 1980s, composite technology was mostly used to construct boats and cars, and these two sectors, more than any other industry, have contributed greatly to developments in this technology. The learning curve for carbon-fibre technology has now peaked and construction is stable. Despite all this being seen as an incredible technical evolution, designers continue to copy structures found in nature. After all, the philosophy behind a piece of carbon laminate is not all that different from a piece of wood: hollow fibres running in one direction. The advantage in using carbon-fibre is that we can shape it at will and its fibres can stretch along the axis of stress. Interesting here, what the yacht designer Roberto Biscontini has to say: “It's no coincidence that we are returning to the elaborate forms seen in nature: there was a reason why things evolved in a certain direction over many millennia. Even in our calculation procedures, we use what is called a ‘Genetic Algorithm' to save time, because it simulates the mechanisms for choosing the right evolution process by comparing the elements. Much like the law of the jungle, which keeps whatever works best. Thanks to the lightning fast computational power of our computers, we can now simulate in a matter of days processes that once took millennia.”
Although they travel differently (cars on land and boats on water / air), the fluidodynamic systems involved in their design are very similar: wings (or fins) are used in cars to create downforce and so keep them in contact with the ground (the ‘ground effect'), while these are used in boats to reduce contact with the water (the ‘lifting effect'). In both cases, the designers are looking to increase speed.
The America's Cup now includes “flying” boats with the capacity to rise above the water like hydrofoils. Their foiled fins dramatically change the resistance they oppose to more conventional ones and thus their velocity: indeed, they can now reach speeds previously only possible in craft built specifically to beat speed records, travelling at nigh on 50 knots, just under 90 km / hour. Not very quick when compared to land speeds, but unbelievably fast when sailing on water. While road speed is very dependent on engine power and a number of other fixed parameters, maximum sailing speeds are closely linked to wind intensity. But structural stress and danger also increase with speed. Furthermore, the wind factor is not the same for all... it can blow at a different speed and in a different direction for competitors just a few metres apart. So, as well as knowing how to get the best out of their craft and the wind, helmsmen also need to know how to direct the boat to where the wind is better. Crucial for top performance are the wing structure, the keel and the trim systems: just a fine adjustment will make the boat pick up speed or slow down. These are key skills when learning to control any sailboat. One of the peculiarities of this edition, however, is that each team now has a boat with a fully automatic system that ‘teaches' the crew how to set the trim and how to behave. There are two areas where the special characteristics of carbon-fibre are best exploited: the truly impressive wing structure and the daggerboards that withstand all the force generated as the boat starts foiling and ‘takes off'.