A smart factory can't exist without the creativity and practical skills of the human race.Because, of course, robotics and automation are dependent on humans. Not the other way around. At the 2016 Festival of Innovation and Science in Settimo Torinese, the focus this year was on robotics, but the unexpected star of the show was man himself. The figure who invented robots, made them work, and most importantly is constantly improving them.The relationship between man and robot, Industry 4.0, factory automation, production processes and the implications that this fourth industrial revolution will have on human workers were the central themes dealt with in a panel discussion featuring Gianni Manchini, Head of Processes and Equipment at Pirelli, along with other executives from Comau, L'Oréal and Siemens. All companies, like Pirelli, with deep roots in the Settimo Torinese area.
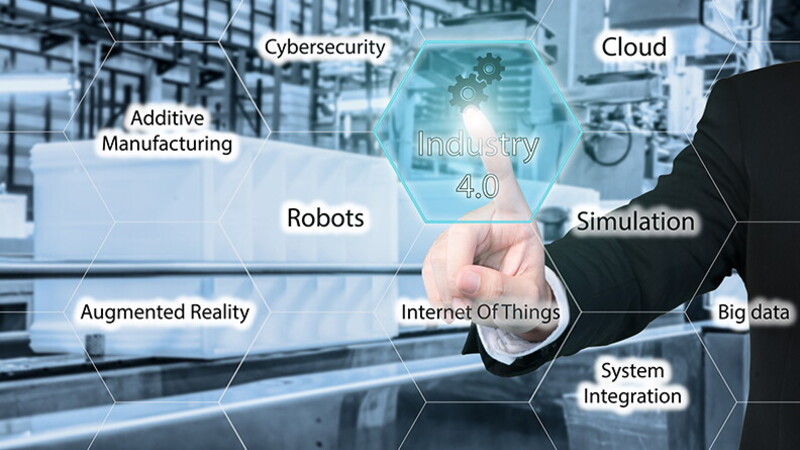
"In the last few years in the industrial centre at Settimo Torinese, just like in the rest of the world, we have invested in human capital," said Mancini in the debate, "And with the introduction of ever more sophisticated and complex machines, we have had to train our employees accordingly, integrating their existing knowledge with new skills used to follow the path to innovation taken by the company."
It is an innovation process made possible by the people who work "on the front line" in the factories, who are able to provide vital suggestions on how to make processes more efficient and productive.The workers at the industrial centre of Settimo Torinese, for example, actively support the engineers in charge to resolve process-related problems and to transfer know-how to other Pirelli production sites all over the globe.
Another determining factor is the valuable collaboration between the company and its suppliers of technology and machinery. Pirelli has a large number of companies who have made their own contribution in terms of innovation and automation, among them Comau and Siemens. One example of successful teamwork between company and supplier is the creation in the Settimo Torinese factory of "Next Mirs", an innovative technology owned by Pirelli and capable of achieving flexible production even for the smallest batches of tyres, and which meets the objective of applying an industrial model which not only ensures high performance, but is also efficient, fast and flexible, able to adapt quickly to different products to be developed and produced.
"Taking innovation to the factory," continued Mancini, "Means introducing machines which help speed up production systems and optimise economic resources, but above all ensure quality and flexibility. The tendency of the market is to make increasingly beautiful products which are ever safer, but at the same time increasingly personalised. This is why it's essential to be able to work alongside partners who are able to adapt their own technology to various product types.".
From mass production to customised production, the latter being the cornerstone of Pirelli's strategy based on the "Perfect Fit": every vehicle model corresponds to a specific tyre capable of providing maximum safety and performance under any conditions.
This level of safety is ensured by the innovative production processes adopted by Pirelli, like VAC, Visual Automatic Control, patented by the company and which enables you to eliminate any margin of error in identifying defects on the tyre. The VAC prototype, winner of the 2015 Masi Prize for Industrial Innovation, is a system which can, via innovative optical systems, "visually" evaluate the tyre and "analyse" it using algorhythms developed by the Research & Development team at the Bicocca laboratories to identify any defect or imperfection. The results are then analysed and any defects found are classified. "The creation of this prototype," explained Mancini, "Doesn't simply limit us to using a machine to do a job that would currently be done by a person, with the difficulties that such an operation brings, but rather allows us to collect vital data which enables us to block defects at origin and predict any imperfections."
It's the Internet of Things at work. A large part of Industry 4.0 involves exactly this: enable machines, robots and human beings to communicate with each other to share data, helping us to not only resolve problems, but above all to predict them and therefore avoid them in the future.It is an objective which is clearly outlined in the strategy of Pirelli, a company which, thanks to the introduction and implementation of a stream of innovative processes, is becoming an increasingly digital company. This is why the Digital Direction group has been created, to work on the development of sensors and also to meet the new needs of the industry, new mobility included, and develop completely digitalised industrial, commercial and management processes, made more efficient and based on predictive models with the help of big data analytics, analysed by a highly-specialised team.
None of this would be possible, however, without the work of the factory workers, technicians and engineers who use their skills to make vital contributions to the development of Industry 4.0, which in turn increases Pirelli's global competitiveness.. With benefits for everybody, increasing the skills of the workers and the quality, innovation and safety of the products.