People, innovation, technology. These are the three words underpinning Pirelli's philosophy and its Pirelli Manufacturing eco-System (PMS). Indeed, the PMS constitutes a set of inspiring principles, methodologies and operating behaviour adopted by Pirelli to fuel its ongoing improvement processes in its production plants and to promote the company's digital transformation.
In the language used by the P Lunga brand, the PMS is translated as “Passion in Operation and Passion in Product”, in other words the strict respect of rules on health, safety and the environment, of product and process standards, it is fueled by the personal occupational passion and digital culture.

The innovation of the PMS is translated as “operational excellence” and is based on the concept of “best achievable performances” and “best practices”. The best solutions identified to improve production flow set new standards and are shared with the other production plants. This way, the new method found, for instance, by Mexican colleagues to replace a drum in Silao (what is commonly referred to as the “pit stop in the factory”) can be suggested to their Romanian colleagues in Slatina and so on to the other factories. Interconnected teamwork where the professionalism of each and every individual is placed at the disposal of others.
Teamwork (people) is in fact essential in a factory where there are plenty of complexities: from the speed at which technology changes and is updated, with an ensuing fast pace of training promoted by the Manufacturing Academy, through to the mixture of products which, at Pirelli, translates as ongoing changes in the set-up of machinery for the production of an increasingly larger quantity of High Value tyres for premium and prestige cars (from Audi and BMW to Lamborghini, Maserati and Ferrari). And where there's a team, there has to be a Captain, an exemplary guardian of factory work, spokesperson and motivator of the members of the team, the person who decides best on their respective roles in the department, redesigns them during the work shift to achieve the best operating performance, which swifts from single to collective in nature.
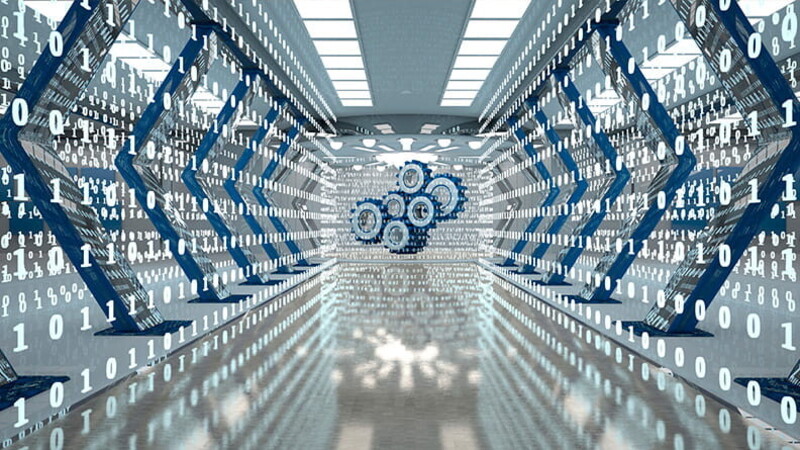
In such a flexible factory, where the focus on technology is so high and where a growing variety of tyres is produced even in very limited batches, in keeping with Pirelli's “tailor made” philosophy, there is a need to solve small or large everyday problems. For this reason, Pirelli organises approximately 200 Kaizen Weeks a year in its 18 Plants; these initiatives are based on improvement, and each time an average of 15 Pirelli workers contribute, each with a different specific skill set. In order to tackle and solve technical difficulties encountered during factory operations, such as a bottle-neck along the material flow, or a repetitive product flaw or a condition of risk encountered, the problem to be tackled is analysed from every perspective until the root-cause is identified, and then all the actions to solve its component aspects are implemented. Thanks to the skills of every individual, constant improvement is thus obtained.
And it is only thanks to shared skills that solutions to the problems encountered can in fact be found. Both intuitive and exciting in creating a spirit of teamwork and operating excellence. This applies both during the Kaizen Weeks and in the operations of every factory work shift, when the workers are increasingly better trained, and can be potentially deployed across several machines in production and thus put into practice their “multi-skill” training to move swiftly from one department to the next, with new digital tools that are technologically sophisticated, without any restrictions on fixed workstations or paperwork, as in the recent past, to guarantee speedy work and exemplary operations.
New skills and new tools, therefore, to grow a factory that works in the present but which keeps its eyes trained on the future. “Manufacturing To Digital”, this is the name of the digital transformation process which Pirelli has embarked upon in its factories; this is the exciting challenge that day after day, shift after shift, brings together our 20,000 workers, the real star players and agents of change.