Come si sviluppa una gomma – Studi mirati, diversi materiali e una definizione accurata di ogni aspetto, sono i passaggi cruciali che portano alla realizzazione di un nuovo prodotto.
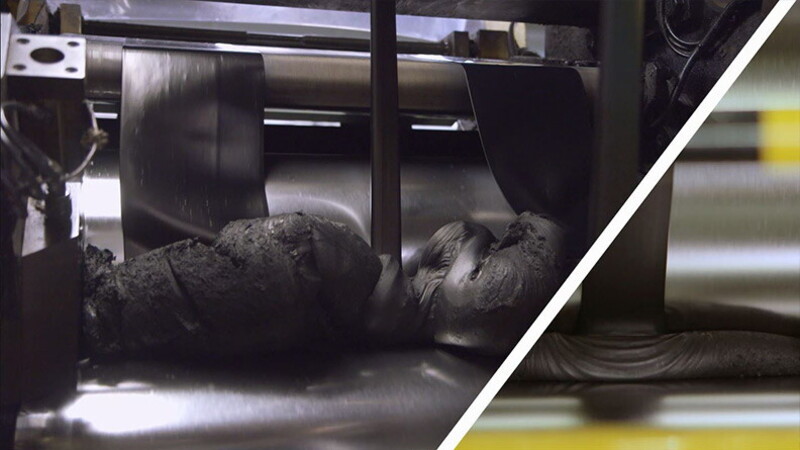
Una mescolatura delle tipologie di gomma, un montaggio con l'applicazione delle varie componenti, quindi un affinamento costante che porta alla forma sempre più definita del pneumatico, costituiscono i diversi passaggi tramite i quali si realizza una mescola.
Il processo, composto da una serie di tappe scandite ed effettuate con attenzione, può comprendere nelle varie procedure anche un numero ingente di sostanze e tipologie di gomme, oltre a fibre metalliche, anche in dose massiccia, che possono ammontare complessivamente a 200 materie e sostanze, come gli additivi, utili nella fase di lavorazione assieme ai tipi di gomme impiegate, sia di origine naturale o caucciù ottenuto tramite il prelievo del lattice da specifiche piante, sia sintetiche. La gomma naturale, considerando la sua struttura molecolare, costituita per circa il 94% da poliisoprene, legato a proteine, acidi grassi e altre sostanze, risulta piuttosto malleabile alle elevate temperature, mostrando proprietà meccaniche piuttosto modeste, per via delle forze abbastanza deboli che legano i polimeri. Le gomme sintetiche, invece, sono frutto di processi di polimerizzazione. Nel caso degli pneumatici, protagonista è il polibutadiene, un polimero del butadiene usato proprio nella polimerizzazione delle mescole.
In una prima fase di lavorazione, possono essere anche più di trenta le tipologie di gomme, tra naturale e sintetica, usate per realizzare e definire un nuovo pneumatico. Materiali che hanno proprietà peculiari e specifiche che differenziano ogni prodotto. La fase di mescolatura riguarda proprio l'utilizzo di queste differenti gomme naturali e sintetiche, fuse e impastate in voluminosi miscelatori. L'accurata lavorazione delle diverse sostanze porta, dunque, a un composto piuttosto compatto e liscio. Successivamente si passa a una fase di assemblaggio, passaggio nel quale sono stabile le caratteristiche del pneumatico prodotto, realizzato secondo precisi criteri qualitativi e specifiche caratteristiche in termini di resistenza e comportamento su strada, sempre tenendo presenti i più alti standard di sicurezza.
L'assemblaggio è un procedimento caratterizzato da ulteriori fasi. Tali passaggi hanno come protagonista un tamburo rotante, sul quale approdano i materiali utili a definire la nuova gomma. In un primo momento avviene l'applicazione di uno strato di gomma sintetica che costituisce la camera d'aria interna delle mescole più avanzate, che non necessitano più di una camera d'aria specifica come in passato. Una volta posta questa si passa alla carcassa, praticamente un'armatura che abbraccia e inizia a definire ulteriormente il prodotto, composta da gomma e una fitta trama metallica. Quindi avviene l'aggiunta dei cerchietti, ai quali è collegata la carcassa. Si tratta di anelli metallici in acciaio che, oltre a garantire impermeabilità alla gomma, la assicurano al cerchio.
La definizione della gomma procede ancora con l'applicazione sui fianchi di fasce di gomma con determinate caratteristiche di resistenza e flessibilità alle deformazioni, che devono supportare le elevate forze a cui sarà sottoposto lo pneumatico in questa area d'azione nevralgica. Con la definizione dei fianchi compaiono anche le marcature che consentono di identificare la tipologia di gomma. La forma propria del prodotto è definita di seguito, quando è gonfiata la zona adiacente al tamburo e prende forma la mescola. Struttura alla quale sono accorpate le tele si sommità caratterizzate dalla trama reticolata che va a definire la carcassa, prima del posizionamento della base che accoglierà il battistrada, cioè la sezione che andrà a contatto con il suolo e che caratterizza ogni specifica tipologia di gomma. Da un battistrada più o meno scolpito, infatti, si riesce a intendere la natura prestazionale del pneumatico.
Poste le diverse componenti, il processo di definizione comunque non è ancora completo. Solo dopo la fase di vulcanizzazione, per intenderci la cottura in un apposito stampo della base preparata, si può avere un'idea più definita del nuovo prodotto ingegnerizzato.
Il cosiddetto “pneumatico crudo” è collocato in un apposito stampo, come citato, per il tempo necessario alla cottura, che ne plasma e solidifica ogni lato. Centralmente, una membrana irrorata di acqua calda, tramite pressione, porta la materia grezza verso le pareti dello stampo e il calore esercita la sua azione. Quindi a 150° prende vita la vera e propria vulcanizzazione della mescola. L'aggiunta di zolfo, consolida i reticolari di polimeri, e il pneumatico acquisisce delle proprietà elastiche oltre a quelle plastiche già presenti.
Terminata la procedura di vulcanizzazione, la fase che consente di comprendere se il prodotto realizzato è conforme o meno a quanto pianificato, è il controllo. Una verifica eseguita tramite l'utilizzo di una specifica strumentazione a raggi X e da un'accurata analisi fatta da ispettori specialisti, consente di rilevare, proprio grazie al meticoloso supporto della tecnologia, se ci siano imperfezioni. Nel caso ci sia anche una minima o impercettibile distorsione rispetto alle caratteristiche richieste, il prodotto è bocciato. Al contrario la definizione del prodotto è completata e si passa a ulteriori verifiche su strada.