In un'azienda come Pirelli, la funzione manufacturing non si ferma mai. Guidata in avanti da un costante processo innovativo, la tecnologia apre nuovi scenari che hanno sempre più protagonisti la digitalizzazione, l'automatizzazione e l'elettrificazione. Insieme a processi di potenziamento delle competenze e riqualificazione professionale, e grazie all'ingresso di nuove risorse nel team, questi elementi collocano Pirelli all'avanguardia nel mondo dell'automotive. Marco Guerrieri, Senior Vice President Manufacturing, spiega quanto possa essere attrattivo lavorare in un dipartimento che coniuga la possibilità di lavorare con le più avanzate tecnologie in un momento di trasformazione delle stesse che non conosce precedenti.
Quali sono le priorità centrali per la funzione Manufacturing?
L'industria manifatturiera sta attraversando un momento di importanti trasformazioni. Sostenibilità, ottimizzazione dei costi e servizi al cliente sono le nuove priorità accanto a quelle più tradizionali di efficienza, qualità e produttività. La digitalizzazione, l'automazione e l'elettrificazione sono elementi centrali, ma le persone sono al centro delle nostre attività.
Sono passati otto anni dall'inizio del processo di digital transformation di Pirelli. Quali sono i cambiamenti che oggi è possibile vedere?
È una domanda interessante, la tecnologia in ambito digital ha dato il via alla “Quarta Rivoluzione Industriale”, sviluppando l'automazione e il potenziale della robotica. Pirelli ha accolto questa trasformazione dal principio e oggi raccogliamo i frutti dell'utilizzo di robot a portale, sistemi di trasporto automatizzati e robot mobili autonomi. Siamo in grado di poter ridisegnare una linea di assemblaggio completamente integrata per ottimizzare il flusso dei materiali, seguire il processo di qualità previsto, ridurre i costi di produzione, rimuovere eventuali ostacoli, migliorare l'utilizzo degli spazi a disposizione e ridurre l'errore umano. La chiamiamo “Future Factory”. Sta diventando realtà nei nostri stabilimenti europei, in particolare in Italia dove avevamo già introdotto una tecnologia di visione per sistemi automatizzati che ci può aiutare a conseguire i nuovi requisiti normativi e a rispondere alle esigenze delle case auto per le quali i nostri pneumatici sono il primo equipaggiamento, oltre a rispondere alla domanda del mercato. La digitalizzazione gioca un ruolo centrale anche nella gestione dell'efficienza energetica, poiché accedendo ai dati di consumo siamo in grado di ridurre in modo consistente il nostro consumo di energia, le emissioni di CO2 e la produzione di rifiuti.
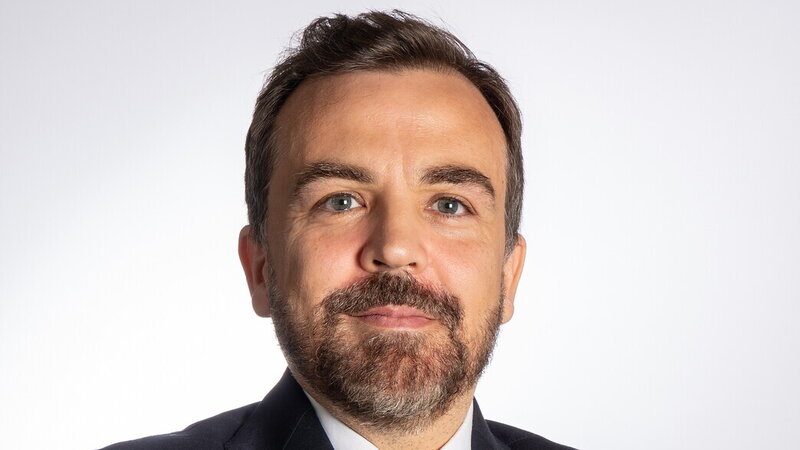
Come è cambiato il lavoro quotidiano delle persone e quali sono stati gli impatti dei percorsi di upskilling e reskilling?
La tecnologia sta trasformando la natura stessa del lavoro e dei luoghi di lavoro. Le persone hanno avuto bisogno di percorsi di upskilling e reskilling perché la tecnologia si sviluppa in tempi molto più rapidi di quelli che consentano alle persone di adattarsi ai cambiamenti. Il nostro dipartimento HR e il Digital ci stanno supportando in questa fase di passaggio attraverso dei training dedicati, in collaborazione con le università, per rafforzare le competenze digitali e costruire una funzione dedicata alla manufacturing intelligence. Questa può sviluppare applicazioni pratiche in ambito digitale in collaborazione con il nostro Digital Solutions Centre di Bari, coinvolgendo nuovi talenti. È importante iniziare a fare nostro il linguaggio del digitale, e il segreto è nel combinare esperienza trazionale e competenze delle generazioni più giovani, che sono native digitali.
Il Piano Industriale 2024–25 menziona la determinazione di 370 milioni di euro in efficienze tra il 2023 e il 2025, la maggior parte delle quali dovute a digitalizzazione e automazione. A che punto siamo?
La dimensione del miglioramento della gestione dei costi è conseguenza di una trasformazione senza precedenti come quella che stiamo vivendo. Stiamo accogliendo tutte le opportunità che la digitalizzazione, l'automazione e l'elettrificazione hanno creato, e sono soddisfatto nel poter affermare che stiamo raggiungendo i target che ci siamo dati nel piano 2024-25. È ancora più sorprendente se pensiamo a quante sfide ed eventi di portata globale stanno avendo luogo intorno a noi.
Quali sono le principali sfide per il Manufacturing nel consegnare nuovi prodotti e incontrare nuove esigenze – come avviene nel caso dei pneumatici Pirelli ELECT tyres per le automobili elettriche o con il CyberTM Tyre?
Le aspettative dei client cambiano rapidamente e affrontiamo un nuovo scenario di mercato altamente competitivo. Oggi, per il cliente, performance significa anche sostenibilità e connettività. I nostri colleghi della Ricerca e Sviluppo progettano prodotti specificamente dedicati ai veicoli elettrici e stanno definendo degli standard per la durata della batteria, il comfort acustico e la durabilità. La sfida dal punto di vista del Manufacturing è dar seguito allo sviluppo del prodotto e garantire i più alti livelli di tracciabilità, funzionalità, replicabilità e qualità. Dobbiamo pianificare la nostra produzione per consegnare ai clienti nel momento giusto, e in questo ci supporta l'Internet of Things, diveramente non avremmo la possibilità di tracciare completamente la filiera, dalle materie prime al prodotto finito.
Quali passi state compiento per portare avanti una Maggiore sostenibilità in ambito Manufacturing?
Ci siamo concentrate molto sull'efficienza energetica, ma mi piacerebbe sottolineare che siamo davvero orgogliosi di essere tra i leader nel nostro settore per l'elettrificazione dei processi di vulcanizzazione. Siamo in fase di phasing out rispetto all'utilizzo del vapore come fonte di energia per tale processo, passando all'elettricità da fonti rinnovabili. Questo passaggio riduce il consumo di energia in kilowatt/ora per pezzo prodotto dell'80% e le emissioni di CO2 dell'impianto del 40%. È un passo fondamentale per sostenere il nostro target di conseguimento della carbon neutrality per il 2030, e abbiamo un piano di rilascio che porterà a convertire tutti i nostri stabilimenti a partire dall'Europa.
Come interagiscono le diverse funzioni aziendali per raggiungere gli obiettivi di Pirelli in relazione all'incremento di materiali di origine naturale e riciclati presenti nei propri pneumatici?
Dobbiamo lavorare a stretto contatto, in parallelo. Un esempio è l'R&D: abbiamo bisogno di seguire lo stesso schema, lavorare alla stessa velocità mentre disegniamo e sviluppiamo nuovi prodotti, o semplicemente non funziona. Lo stesso vale per la Supply Chain; abbiamo bisogno di lavorare insieme per capire come sono gestite le materie prime, come ad esempio avviene per la gomma naturale certificata dal Forest Stewardship Council. Allo stesso tempo, dobbiamo comprendere I loro bisogni per gestire la complessità e riuscire a consegnare un'altissima varietà di prodotti.
Quante persone lavorano nel Manufacturing e quali sono le qualità che ricercate nell'assumerle?
Nel dipartimento Manufacturing lavorano circa 21 000 persone nei nostri 18 stabilimenti, tra Europa, Nord America, Asia e Sud America, per cui in buona parte del pianeta. Cerchiamo persone che abbiano passione per il mondo dell'automazione, persone con un DNA digital. Tutte le nostre persone sono orgogliose di lavorare in Pirelli, sono orientate al risultato e, senza dubbio, hanno solide competenze tecniche. Solitamente provengono da un percorso universitario tecnico, con un background ingegneristico. In media le persone stanno in Pirelli circa 18 anni, e ci piace aiutarle a costruire il proprio percorso di carriera sin dall'inizio, per cui in questo momento la nostra ricerca si focalizza su profili di ingegneri neolaureati.
Il nostro lavoro non potrebbe essere svolto senza il contributo di un team così competente, esteso in tutto il mondo e costituito da uomini e donne di talento – a questo proposito, cerchiamo di includere un numero crescente di donne in un ambiente che a lungo è stato in prevalenza maschile.
Come riuscite a mantenere un approccio coerente nel lavoro in ambito Manufacturing tra così tanti siti in diversi continenti?
È un'enorme sfida. È essenziale sviluppare un linguaggio comune, standard e metodologie, e condividere la stessa cultura industriale. Questo è l'obiettivo del nostro programma Pirelli Manufacturing Excellence, che include percorsi di sviluppo e attività di formazione. Inoltre offriamo a tutti gli stabilimenti gli strumenti per sviluppare i propri programmi di riduzione costi all'interno del metodo di lavoro sviluppato da Pirelli. Viaggiamo regolarmente per visitare le nostre unità operative e abbiamo degli incontri annuali a livello globale nei quali abbiamo modo di incontrarci e rafforzare le nostre relazioni, perché il fattore umano è fondamentale.
Perché lavorare in Pirelli?
Avere a che fare con tecnologie all'avanguardia è da sempre parte della nostra storia, e stiamo affrontando una trasformazione tecnologica senza precedenti. Siamo appassionati del nostro lavoro. Penso che lo sforzo compiuto nei campionati sportivi sia un chiaro segno di questo. Così come il nostro impegno nell'America's Cup, o quello espresso dal progetto del Calendario. Ognuno di loro sottolinea in modo diverso il nostro orgoglio di lavorare in Pirelli e le molteplici opportunità che questa azienda ci offre.